Adrian Tippins of Custom Made Arrows starts a series of features on how to build a perfect set of matched arrows. Step one is shaft preparation
In the first part of this “how to” series, we will be looking at the various processes that shafts have to go through before they can be used to make a set of final arrows. We’ll call this shaft preparation. Remember the old saying, “fail to prepare, prepare to fail”? This is very true of arrow building. Ultimately, the success of the end product will be a direct representation of how well we prepare from the start and how much patience and application we give the project. Getting a good bond on vanes, points, pins and anything else glued in or on the shaft requires the surfaces to be squeaky clean. A good tip before you start is to invest in some latex gloves to stop the transfer of oil from the skin to the arrow or other components. The gloves will also protect your hands from any chemicals, glues and solvents.
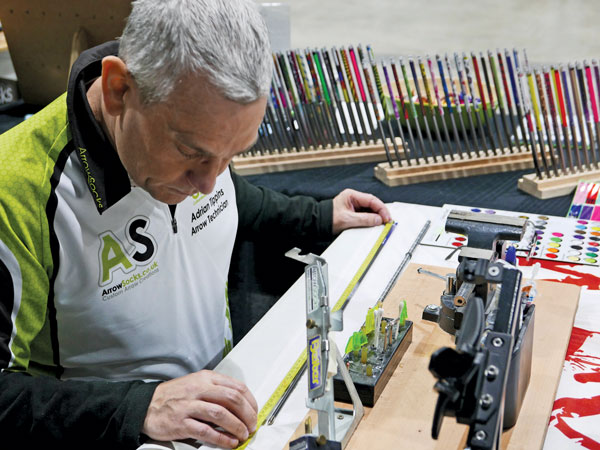
Step 1
First things first – your arrows need to be the right length, so check out the AMO to make sure they don’t need further cutting
First of all, your chosen spine of arrow shaft must be cut to the right length. Length is measured from the groove of the nock to the end of the shaft excluding any points or inserts. This is known as the AMO (Archery Manufacturers Organisation) length. This is the format that all shops and arrowsmiths will use when cutting arrows. As nocks and nock pin hardware can differ in length, it’s advantageous to let the arrowsmith know what nock system is going to be used so that the AMO length can be measured with those particular parts. If this information isn’t communicated, recurve shooters often find they have to move the position of their clicker to compensate for the small difference in nock length, or the quarter inch approximation that some establishments will use when measuring and cutting arrows. Perfection requires precision, and precision is always preferable to approximation.
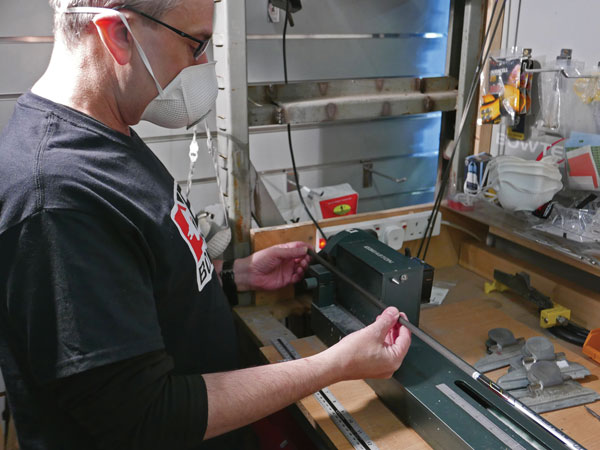
Step 2
If an arrow does need trimming, a professional arrow saw is best for creating neat, clean ends
For accuracy and safety, arrows should always be cut on a proper arrow saw to attempt to cut the arrow as clean, square and as neat as possible. I have heard of people using a pipe cutter to trim aluminium arrows down, however, this method is prone to creating discrepancies in length within a set, and also produces a rough mating edge with the point. Carbon arrows need to be cut at a high speed of at least 5000rpm – 8000rpm and above is preferred, though – with an abrasive blade, not a toothed one. Do ensure that you take adequate safety measures when cutting arrows and use face marks and eye protection. Dust extraction systems are also very handy to save you cleaning up piles of carbon dust!
Contrary to popular belief, all arrows are cut from the front, even barrelled arrows. The one exception is the Easton Triumph arrow. Cutting arrows from the rear can affect the spine on some models and you will definitely lose the honed factory edge for precise mating of nock pin adapters and nocks if they are trimmed from the rear. After the arrow is cut it should be de-burred and the edges finished ready to receive a point.
Now that the shaft is of the correct length, we now have to clean it for fletching and the insertion of any hardware to maximise the internal and external bonds. The shaft should be cleaned both inside and outside to remove any manufacturing residue, dust from cutting, or oil transfer from our hands. To clean an arrow internally, use a cotton swab soaked in 100 per cent pure acetone or IPA (Isopropyl Alcohol). Repeat the process until the cotton swabs remain clean. It’s important to use 100 per cent pure solvents as these will not themselves leave any residue behind. Pure solvents should evaporate very quickly and not need any physical drying.
Shafts need to be cleaned externally with mild detergents prior to fletching as they arrive with the end user full of contaminants from the factory and manufacturing process. This is the most overlooked area of arrow building, as people often think their new shafts are ready to go. The truth of matter is that new shafts are totally filthy and require studious attention to prep them for use. Shafts should ideally be cleaned, rinsed and air dried. Getting this step right will greatly help with fletching adhesion when the time comes, especially if you’re planning on fletching directly to the bare shaft.
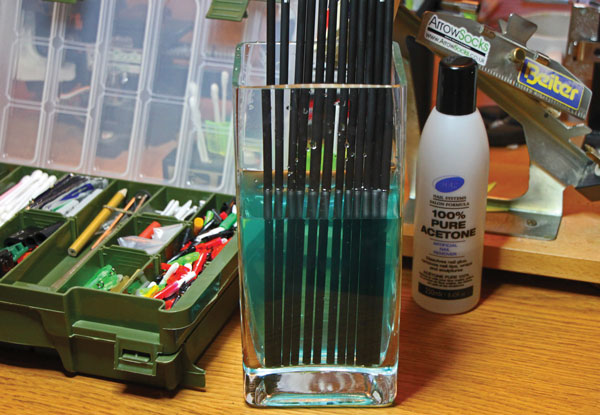
Step 4
Cleaning the shafts externally will help with fletching adhesion, particularly if you’re fletching directly onto the shaft
Even if not, cleaning will also help wraps to stick far better, too. I have found AAE Max Clean and SSR from Bohning to be the most effective cleaners. Simple Green detergent is also very good. Please refer to manufacturers’ guidelines for application details and soaking times. If you’re in a hurry you can wipe the arrows down with a pure solvent prior to fletching, but be aware this can have a negative effect on fletching glues. Try to use clean cotton cloths or rags for cleaning as some kitchen towels and tissues have chemical sizings on them to help keep the layers together. Solvents can dissolve these and contaminate the surface of the arrow. This cleaning step is especially important for A/C arrows that are porous and can harbour contaminants in the surface. Do be patient and allow the shafts to air dry as rubbing them with towels and so on can transfer film or fibres from the towel to the shaft.
Getting vanes to stick directly to shafts is not as easy as it first sounds, and this is especially true in the case of bonding vanes directly on to aluminium arrows with anodised finishes. The modern day anodised finishes are tantamount to a non-stick finish. This is great for helping the arrow to come out of the target easily, but not good for bonding vanes to. The best way around this issue is to apply a wrap, which is something that we will be looking at in another “how to” feature later on.
If you must bond vanes directly to the shaft, the best way to ensure good adhesion is to give the glue a key to stick to. This is done by gently abrading the shaft. Mark exactly where the front and back of the vanes will come to on the shaft with a Sharpie or similar pen that can write on smooth shiny surfaces. Next, mask off the arrow, leaving the window for the vanes visible. With ultra fine grade 00 steel wool or similar abrasive paper, set about dulling the visible window which a gentle circular motion. You’re not looking to sand the anodised coating off completely, just take away the sheen to a lightly dulled finish. This step will need to be done prior to the external shaft cleaning with detergents.
Fletching directly to most full carbon arrows such as X-Busters should be a relatively simple task as these shafts tend to have a laquered finish, which is essentially plastic. Vanes stick very well to this and the shafts can simply be wiped down with a damp cloth and air dried prior to fletching. The internals will still need to be swabbed as detailed above before the hardware gets installed.
Next week we will be taking an in-depth look at the installation of hardware and the application of wraps and decals.
Find Part 2 of Adrian Tippins’ series here
This article originally appeared in the issue 116 of Bow International magazine. For more great content like this, subscribe today at our secure online store www.myfavouritemagazines.co.uk
Can u use one of those small cutters they are only about 7pound of amazon and about 5 inches high they cut from 3mill to 22mil u place the arrow in the tool on the to wheels then tighten it up a bit then turn it keep on tighten it up as you turn the cutter till it cuts through. I had an old one and tried it with an old arrow even though the blade was a bit blunt it cut straight but at the end of the cut it would ov needed a little rub with sand paper but with a new one it should b OK won’t it. Thanks for some advice pls.
Hi Graeme – will answer this in the next edition of the magazine.